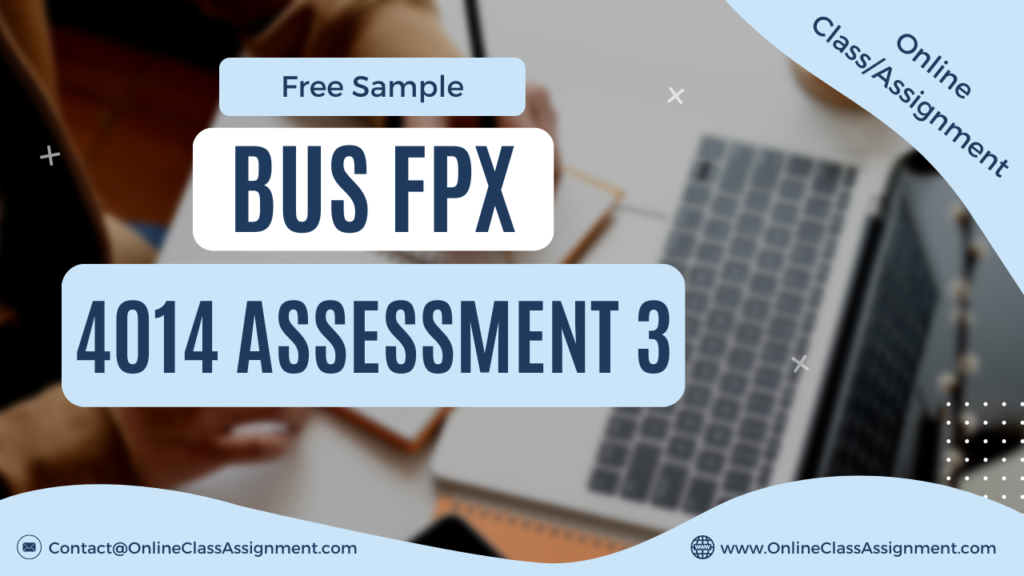
BUS FPX 4014 Assessment 3 Supply Chain Decisions
Student Name
Capella University
BUS-FPX4014 Operations Management for Competitive Advantage
Prof. Name
Date
Interview with a Supply Chain Manager
I conducted an interview with a Supply Chain Manager from an online retailer, who opted to maintain anonymity. Emphasizing the significance of supply chain and operations management, they highlighted its critical role irrespective of a company’s size. Supply chain management, whether for products or services, is vital for organizational success. The interview covered the following aspects:
Importance of Supply Chain Management:
- A successful supply chain management system enhances operational efficiency, leveraging available tools and resources to boost profits by reducing operating costs. Smooth operations lead to increased customer satisfaction and higher product turnover.
Operations Management Tools:
- Forecasting tools utilize historical data to predict future needs and demands, aiding in product and service offerings, staffing, production, and inventory management.
- Shipping status tools provide real-time updates on shipments, enabling prompt adjustments to any issues encountered.
- Statistical reasoning tools assess the likelihood of errors before occurrence, empowering organizations to preemptively address potential issues.
Alliances and Partnerships:
- The company has numerous strategic alliances and partnerships across diverse industries and markets, aimed at mutually beneficial resource-sharing.
Component and Material Acquisition:
- The company employs a Material Requirements Planning system to track inventory and demand concurrently, reducing response time and ensuring adequate materials for production.
Integration of Component Parts:
- The production process follows a clear set of guidelines starting from production planning, ensuring availability of necessary materials before production commences.
Key Tradeoffs of Just-in-Time (JIT) Manufacturing:
- JIT manufacturing offers cost savings, reduced warehouse space requirements, and minimized wastage. However, it is susceptible to material price fluctuations and supply shortages.
Key Tradeoffs in Outsourcing Decisions:
- Outsourcing can enhance efficiency and lower labor costs, especially during periods of increased demand. However, it may pose security risks, loss of control, and reduced quality.
Scenario Analysis
ABC has determined internal manufacturing costs for a new valve product amount to $27,000 in fixed costs (FC) and $8 variable costs (VC) per unit. The company anticipates selling 4,800 units annually. Jay Production, a reputable outsourced manufacturing company, offers to produce the valve for an annual fee of $29,000 plus $6 per unit. Based on the calculations below, outsourcing to Jay Production proves more cost-effective:
Total Annual Manufacturing Cost for ABC:
- TC = $27,000 + ($8 * 4,800)
- TC = $65,400
Total Annual Manufacturing Cost for Jay Production:
- TC = $29,000 + ($6 * 4,800)
- TC = $57,800
BUS FPX 4014 Assessment 3 Supply Chain Decisions
Get Capella University Free Business Samples
BUS FPX 3007
BUS FPX 3011
BUS FPX 3021
BUS FPX 3022
BUS FPX 3030
BUS FPX 3040
BUS FPX 3050
BUS FPX 4012